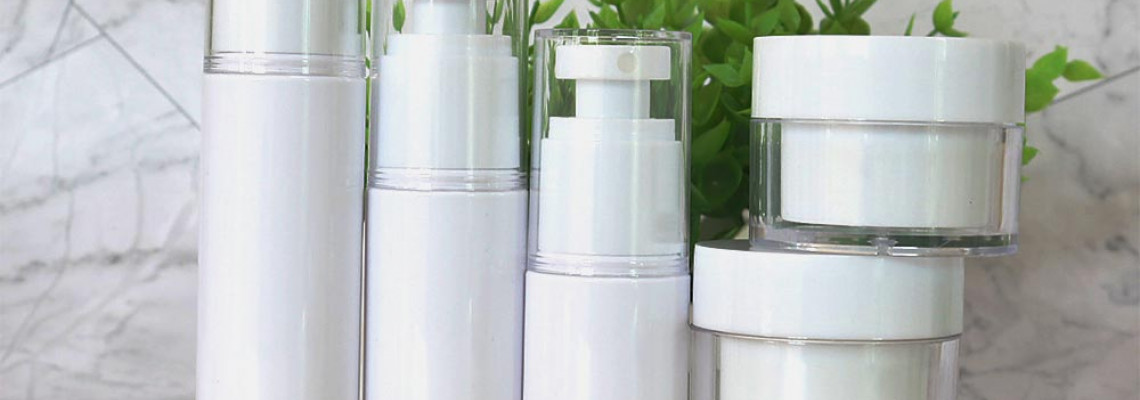
The Ultimate Guide on cosmetic packaging materials
Common cosmetic packaging material have:
color box: color box - is a folded paper box and micro corrugated cardboard box made of two materials: cardboard and micro corrugated cardboard. Companies that produce paper boxes are called color box printing and packaging factories, referred to as color box factories.
Film bag rolls / film bags: aluminum foil bags are made of a variety of plastic film laminated after the combination of the bags made by bag-making machine later, used to package cosmetics, daily necessities, etc..
label: cosmetics common self-adhesive label, a material, also known as self-adhesive material, is a composite material with paper, film or other special materials as the fabric, coated with adhesive on the back, with silicon coated protective paper as the backing paper. Self-adhesive is the collective name of materials with this type of nature.
Carton: Carton is the most widely used packaging products, according to the different materials, there are corrugated boxes, single-layer cardboard boxes, etc., with a variety of specifications and models. Cartons commonly used three layers, five layers, seven layers used less, each layer is divided into lining paper, corrugated paper, core paper, surface paper, lining, surface paper with tea board paper, kraft paper, core paper with corrugated paper, a variety of paper color and feel are different, different manufacturers produce paper (color, feel) is also different.
plastic bottles: plastic bottles are mainly made of materials such as polyethylene or polypropylene and added with a variety of organic solvents. Plastic bottles are widely used polyester (PET), polyethylene (PE), polypropylene (PP) as raw materials, after adding the corresponding organic solvents, after high-temperature heating, through the plastic mold after blow molding, extrusion, or injection molding of plastic containers.
glass bottles: glass packaging containers are made of quartz sand, limestone and other silicate materials after high-temperature calcination and fusion, the temperature reaches nearly 1,000 degrees (1,600 degrees), into a liquid, through the mold molding, and then after annealing and cooling processes, made
cosmetic tube: cosmetic tube with light quality, easy to carry, strong and durable, recyclable, easy to squeeze, processing performance and printing adaptability, etc., by many cosmetic manufacturers, widely used in cleansing products (facial cleanser, etc.), skin care products (a variety of eye cream, moisturizer, nutritional cream, snow cream and sunscreen, etc.) and hairdressing products (shampoo, conditioner, lipstick, etc.), etc. Cosmetics packaging. 8.
penicillin bottle: also known as borosilicate glass or soda lime glass control (molded) injection bottles, is a kind of rubber stopper and aluminum-plastic combination cap sealing small bottles. Early penicillin is mostly used to contain, so the name of the bottle, cosmetics are mostly used in the packaging of lyophilized powder.
ampoule bottle: the original English meaning of concentrated essence, often used in the efficacy of serum packaging.
Disposable bottle: the Disposable means "one time and throw away". Of course, many bottles are "daily", "a day a throw". The packaging of this skin care product is not quite like the bottles we normally use for skin care products, the disposable bottle is generally used for the packaging of the tube. This packaging technology is called B.F.S. The Chinese name of B.F.S. can be interpreted as medical aseptic filling technology. This technology is usually used in the packaging of eye drops, injectable drugs, etc.
1. Color Box
1. 2、 Common materials of color box
White cardboard, gold and silver card, double copper paper, kraft paper.
1.2.1 White cardboard:
white cardboard is generally distinguished as: blue and white single and double-sided coated cardboard, white bottom coated cardboard, gray bottom coated cardboard. Completely bleached chemical pulp manufacturing and full sizing of single-layer or multi-layer combination of paper, suitable for printing and product packaging, the general quantitative in 150g/m2 or more. The characteristics of this cardboard are: high smoothness, good stiffness, neat appearance and good evenness.
1.2.2 Gold and silver cardboard:
Gold and silver cardboard is coated with a layer of UV oil on the surface of the paper through a rubber blanket using UV transfer technology, and then the light column film or special order pattern is transferred to the top of the printed paper through a roller.
Double copper paper: It refers to double-sided copper paper. Double-sided coated paper is a kind of coated paper, that is, coated on both sides, both sides have a good smoothness. Copperplate paper also includes single copper, sub copper, high gloss copper, art copper and so on.
Kraft paper: Kraft paper generally has a rough surface and high strength. It is usually yellowish-brown in color. Semi-bleached or fully bleached kraft pulp is light brown, cream or white.
1.3、Common process of color box
-Stamping gold and silver: stamping gold and silver customer specified location stamping on gold, silver or other colors, a LOGO stamping gold and silver general charge of about 0.08 yuan / color, if it is a large area stamping gold and silver need to receive 0.15-0.2 yuan / one.
-Local UV & Reverse UV: According to the needs of product varnishing, local varnishing coating is applied to the parts of trademark and packaging printings that need to be highlighted, the varnishing pattern looks bright, shiny and three-dimensional compared with the surrounding patterns, which can produce unique artistic effects. Generally a color box partial UV needs to charge 0.05-0.08 RMB/color box.
-stamping: is the use of convex mold plate in the case of pressure, the printed material to make the surface has a three-dimensional feeling, generally in the white card will be used with hot stamping, hot silver, UV use this process, generally striking a color box is charged 0.05 yuan / a
-varnish: in the finished graphic printing copy surface, using the printing machine once on the varnish, so that the printing surface to obtain a bright film layer method, enhance the light resistance of the ink, heat and moisture resistance, play a role in protecting the print, beautify the product; this process is low-priced, does not increase the additional cost, in foreign countries is also an environmentally friendly process
-Polishing oil: refers to the printing of the paper to be dried, the process of hot pressing and cooling the finished product by the calender hot roller, is the deep processing process of varnishing, can make the coating more dense, smooth, high gloss brightness of the ideal mirror effect. This process is easy to appear in dry weather; generally a polished box needs to charge 0.03 yuan/each.
Frosting: Frosting is a process to make the original smooth surface of an object not smooth, so that the light shining on the surface forms a diffuse reflection.
Embossing: It is a common decorative packaging material processing process. According to the embossing method, it is divided into flat embossing and roller embossing. Embossing process is a kind of art processing technology that uses a mold with concave and convex pattern to deform the surface of decorative packaging materials (PVC, aluminum, wood, paper, etc.) under the effect of certain pressure and temperature to form a certain pattern.
2. the film bag coil / film bag for detergent
From Material: aluminized, pure aluminum of film
From Surface effect: for glossy, matte surface.
From Bag shape: shaped bags, suction mouth bags
2.1 Irregular Shaped bags:
shaped bags are not the conventional four-square bags, but present irregular shapes. Shaped bags have excellent shelf appeal with their variable shape, and are a more popular form of packaging in foreign markets. Generally shaped bags need to charge the customer USD$100 / color version fee, but also need to charge the mold fee.
2.2 Suction nozzle bag:
Suction nozzle bag is also called pot nozzle bag suction nozzle bag is an emerging beverage, jelly packaging bags based on the development of stand-up pouches, now also used in cosmetics. Minimum order must be 50,000 (13 * 9.8CM); this bag generally requires a mold fee of USD100/ color
3. Labels
Label commonly used materials are divided into paper and plastic film class two, now according to the new regulations small capacity cosmetics can also be set up electronic tags.
Paper Label : mirror coated paper, die paper, copper plate paper, synthetic paper, kraft paper, thermal paper
Plastic film category: PET, PE, OPP, BOPP label.
3.1、paper Labels.
Grassian paper: good strength, light transmission, suitable for barcode printing and automatic labeling, but easy to curl, not suitable for flat sheet printing
Kraft paper: suitable for sheet printing, not suitable for barcode printing and automatic labeling
Transparent film: the highest smoothness, suitable for particularly high demand for transparency, high strength suitable for ultra-high speed labeling
Module paper characteristics: printing, processing good suitability of non-coated paper surface roughness, strong oil absorption, generally do not need to add protective film. Can be used for laser printing.
coated paper characteristics: coated paper is also known as coating paper, this paper is coated with a layer of white pulp on the original paper, after calendering and made. Basic grammage 80g/m2, the use of temperature range -50 ~ +90 degrees, the minimum labeling temperature +7 degrees, suitable for thermal transfer printing. Copper plate material is generally divided into: mirror copper and copper plate paper
3.2、Synthetic paper
Synthetic paper characteristics: PP synthetic paper is made of polypropylene resin, polyethylene resin and natural stone powder and other major raw materials mixed pressed from a synthetic paper. Identification: one direction can be torn, the other direction can not be torn
PE characteristics: high-gloss transparent polyethylene film, good printability and die-cutting properties, excellent flexibility, suitable for often extruded bottle type. PE material is generally divided into: transparent PE and light white PE
3.3、Labeling process
Labeling process often has: letterpress offset printing flexographic printing gravure printing screen printing hot stamping varnishing lamination
3.3.1 Letterpress printing:
letterpress printing self-adhesive labels, printing plates for photopolymer letterpress, printing labels with the advantages of full ink color.
3.3.2 Offset printing:
offset printing is characterized by fine graphics, rich layers, suitable for high-volume printing, and printing equipment can be used for multiple purposes, but the sheet offset printing is not suitable for printing the surface without absorbent film, because the film label is mostly roll to roll printing, the need for volatile drying ink. Offset printing can be printed thicker plastic materials, such as in-mold labels, labels tags, but the machine must be retrofitted with uv curing device, requiring a considerable amount of money.
3.3.3 Flexographic printing:
the current quality of flexographic prints is no less than offset printing, and even has its own unique place. The advantages of this printing process is the simple structure of the machine, low cost, printing quality can be comparable to offset, gravure, and has the advantage of thicker ink layer than offset products, flexo printing using water-based ink and uv ink, not polluting the environment. However, due to the greater flexibility of flexo, order reproduction and gravure and ordinary letterpress different, flexo printing highlights to the middle tone of the dot increase is larger, the printing contrast is small, the highlight level is prone to fault, in the printing of fine graphics label, in order to make up for the level of defects, the highlight part can be used to FM dot, dark or middle call amplitude plus network to improve quality. No flexographic printing machine label printing plant can be introduced specifically for self-adhesive label printing laminated narrow width flexographic printing machine, this printer is suitable for film label printing.
3.3.4 Gravure printing:
gravure printing using a short ink delivery system ink supply, web printing, a high degree of automation, the use of solvent-based ink, ink drying quickly, is the first choice for film-based printing. General gravure printing machine speed is high, many gravure printing machine rear end is also equipped with cylinder die-cutting device, can be die-cutting, creasing, suitable for a variety of label printing. However, due to the gravure plate making cycle is long, expensive plate making costs, only suitable for high-volume label production.
3.3.5 Screen printing:
screen printing is the most widely adapted to the substrate printing method, at present, there are many screen printing factory using low cost screen printing equipment to undertake self-adhesive labels and film label printing business. Screen printing labels are characterized by strong ink color, three-dimensional sense, can be printed with uv ink film products. In addition to a handful of several rotary screen printing equipment can be competent volume to volume label printing, most screen printing equipment for semi-automatic flat screen printing machine, can only print a single product, overprint accuracy is not high, not suitable for film label production equipment with the production line.
3.3.6 Hot stamping:
as an important metal effect surface finishing method, is an effective way to enhance the visual effect of trademarks, cartons, labels and other products, widely used. Hot stamping and cold stamping these two main stamping methods have advantages and shortcomings, in practice, according to the specific circumstances to choose the appropriate stamping method, mainly based on cost and quality considerations. According to the processing method of self-adhesive labels, its hot stamping method is divided into sheet-fed hot stamping and roll paper hot stamping. Sheet-fed hot stamping to the traditional hot stamping process the same, in the special hot stamping machine processing. Roll paper hot stamping is done on the label linkage machine, is the most widely used a processing method. Roll material stamping has the following ways: ① labeling machine on the flat pressing flat stamping ② multi-station flat pressing flat stamping ③ processing machine on the flat pressing flat stamping ④ rotary machine on the round pressing round stamping ⑤ rotary machine on the cold stamping
3.3.7 varnishing:
varnishing process is mainly applied to the mirror coated paper, coated paper type label surface coating, the purpose is to increase its surface gloss, and to achieve the role of anti-fouling, anti-humidity, protection pattern. According to the processing method, the varnishing of self-adhesive label material is divided into sheet varnishing and web varnishing, of which web varnishing is the most commonly used method in the self-adhesive label printing process. Roll paper self-adhesive label varnishing is carried out on the wheel transformation labeling machine. UV varnishing process is commonly used, that is: after the printing of the pattern surface evenly coated with a layer of UV varnishing oil. For water-based ink flexographic labels, varnishing is an essential process.
3.3.8 lamination:
backing paper composite film composite - on the label machine, lamination principle with the backing paper composite film composite process is basically the same. Bottomless paper film by its own material surface smoothness (surface tension) after rewinding instead of the backing paper, adhesive with its surface bonding, but also peel, and no residual adhesive traces. The material used for bottomless paper film is BOPP film with low surface tension. Bottomless paper film lamination cost is low, is currently the most widely used a laminating material.
Stamping material square 3 yuan, cold stamping: length X width X USD$0.5= material cost. The cost of hot stamping is about to add 0.01-0.02 USD / sheet
UV cost probably need to add 0.004-0.005 USD / sheet. Hot stamping will have printed cold stamping no, but from the surface effect or hot stamping glossy better; but hot stamping large area hot words pressure to be very large, hot not real, easy to have burrs, vapor bubble point, negative force is not good, and hot gold powder will be used to scatter the image; and cold stamping can be printed directly after the other colors, large area hot gold and silver and then printed content is very advantageous, but the cost is high;.
4. carton
Carton commonly used three-layer, five-layer, seven-layer use less, each layer is divided into lining paper, corrugated paper, core paper, top paper, lining, top paper with tea board paper, kraft paper, core paper with corrugated paper, a variety of paper color and feel are different, different manufacturers produce paper (color, touched feel) is also different.
Different corrugated shapes are bonded into corrugated board with different functions. Even if the same quality of top and lining paper is used, the difference in flute shape makes the performance of the corrugated board different. Internationally, there are four types of corrugated fluting: A-flute, C-flute, B-flute and E-flute. Their technical specifications are different
Commonly used styles of cardboard boxes nowadays: ordinary flat boxes, keyed bottom boxes, airplane boxes
5. plastic bottles for cosmetic
Plastic bottles are mainly made of materials such as polyethylene or polypropylene and added with a variety of organic solvents. Plastic bottles are widely used polyester (PET), polyethylene (PE), polypropylene (PP) as raw materials, after adding the corresponding organic solvents, after high temperature heating, through the plastic mold after blow molding, extrusion, or injection molding of plastic containers.
Material: PET, PE, PP, ABS, AS, acrylic
PET: environmentally friendly materials, can be in direct contact with the material, advantages: high barrier, light, non-breakable, high transparency, soft material. Disadvantages: not resistant to high temperature, easy to change shape above 40 degrees.
PE: environmentally friendly materials, can be directly in contact with the material body, a molding, direct injection out of the finished product, the surface matte, not as bright as PET, the caliber is more rough, can not do transparent effect, PE material surface treatment is not suitable for spraying, can not be colored, easy to fall, screen printing need special overfire treatment.
PP: environmentally friendly materials, can be in direct contact with the material, low density, strength, stiffness, hardness and heat resistance are better than PET, can be used at about 100 degrees, but low temperature becomes brittle, not wear-resistant, so generally used for cosmetic lids preferred materials.
ABS: good strength, good toughness, easy processing molding thermoplastic polymer material, its high strength, corrosion resistance, high temperature resistance, so often used in the shell of the product, processing of the product surface clean, easy to dye and electroplating, some need to do electroplating cover are generally selected for this material. Some double-layer skin care and beauty bottles are also commonly used to this material.
AS, ABS: AS transparency is better than ABS, and better toughness.
Acrylic: material for injection molding bottles, chemical resistance is poor, generally can not be directly filled with cream, need to match the liner barrier, filling is not easy too full, to prevent the cream into the liner and acrylic bottle between, so as not to crack, transportation in the packaging requirements are high, because the scratch looks particularly obvious, high permeability, the sense of the wall is particularly thick, but the price is quite expensive.
Plastic bottle bottom material sign logo:
Plastic bottle surface printing treatment craft charge details:
Surface treatment | fee it cost | Remark |
---|---|---|
Hot stamp gold/Silver | 0.02usd | depend on size |
Satin/Mat | 0.05-0.25usd | depend on size and bottle shape, and color |
silk-screen printing | 0.01usd | per pass of bottle per color |
labeling | 0.010-0.017 | refer the silk-screen printing |
6. glass bottles
The manufacture of glass packaging containers is the quartz sand, limestone and other silicate class materials through high-temperature calcination and fusion, the temperature reached nearly a thousand degrees (1600 degrees), into a liquid, through the mold molding, and then after annealing and cooling processes, made; glass bottles are generally classified by material color, divided into: fine high white, high white, general white, green material, tea material, etc.
Glass bottles are generally formed by blowing and pressure blowing method, the blowing method is generally suitable for narrow-mouth bottles, such as water and milk type of bottle shape, pressure blowing method is generally suitable for wide-mouth bottles, such as cream bottle shape.
Glass bottle product process is also called glass bottle deep processing, refers to the glass bottle surface or the inner wall of deep processing, such as: sand masking, silk screen, hot stamping, spraying, electroplating, polishing, etc., so that the surface of the glass bottle to present different technological effects
-Glass bottle screen printing
Screen printing commonly used in daily use for high temperature screen printing, low temperature screen printing
Low-temperature screen printing is the ink for the oil, after printing after about 150 degrees of low-temperature baking; some screen printing is not required after baking, printing is completed naturally placed to dry; the advantage is the color diversity, ink stability, color difference is small, the design is difficult, such as mesh or finer text to achieve better printing results, the disadvantage is that the ink negative force is not strong, easy to rub flowers, touch flowers;.
High-temperature screen printing is the ink for the powder foam, after printing need to go through 550-700 degrees of high temperature baking, the advantages of friction resistance, not easy to lose color, strong adhesion, vivid colors, more vivid color; its disadvantages: the color is limited, easy to produce color difference, part of the color of high temperature screen printing can not do a good job, such as purple, too fine text and lines can not be better shown; !
7. cosmetic plastic tube
plastic tube commonly used materials: aluminum plastic tube, PE plastic hose, all-plastic tube, encapsulated aluminum plastic tube
Aluminum-plastic tube: ordinary sheet, high-gloss sheet, lei shot sheet hose.
PE plastic tube: two-layer composite hose, five-layer composite hose
All-plastic hose: single-layer and multi-layer (2-7 layers) according to different materials, with different barrier properties, surface printing effect network than PE plastic hose better
8. pump and cap accessories for plastic bottles, glass bottles.
the matching cosmetic bottle accessories generally plating, plastic-based, mainly embodied: pump head, lid, inner plug, outer cover, dropper, etc.
Matching composition:
1, lid + inner plug
2、Pump head + outer cover
3、Drip tube + shoulder cover + latex head
4、Lid + hand pull pad + inner liner